Мотокофры GIVI.
24.02.2021 12:24:00
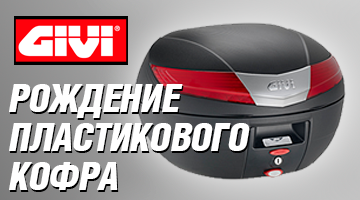
Рождение пластикового кофра Givi. Путь от скетча до магазина.
- Giuseppe Visenzi (Джузеппо Висенци) основал свою компанию в 1978 году. Название Givi образовано от первых букв имени и фамилии – просто и скромно. На данный момент Givi – это 10 заводов, складов и офисов, в которых трудятся 800 человек.
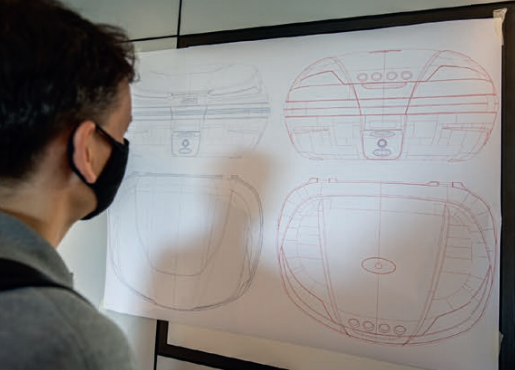
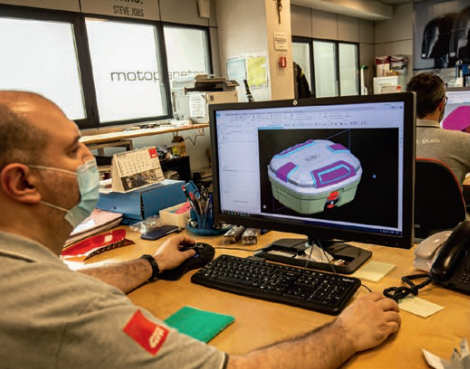
Над созданием новых продуктов в головном офисе компании работают три дизайнера и шестнадцать инженеров. Путь нового кофра к покупателям начинается с набросков обычным карандашом на обычной бумаге. Постепенно вырисовывается облик. Только после того, как эскизы будут одобрены, они отправляются в студию 3D-моделирования, где будущий мотокофр будет сотворён в электронном виде. После чего на станке с ЧПУ его можно будет выпилить в масштабе 1:1 из большого куска дерева.
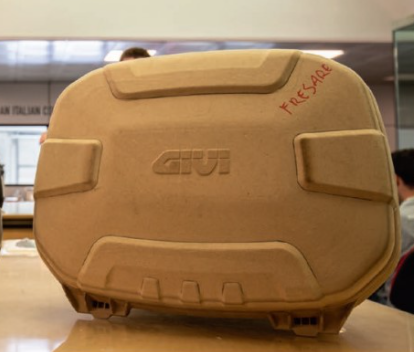
Деревянную модель мотоциклетного кофра после полировки и выведения идеальной формы сканируют для создания финальной 3D модели. В это же время к процессу подключаются специалисты, ответственные за фурнитуру – они работают над механизмами замков, светоотражающими элементами, накладками, петлями, уплотнителем. В результате должны получиться компьютерные образы литьевых форм, в которых будут производиться мотокофры.
Запускается процесс испытаний первых предсерийных кофров на прочность корпуса и отказоустойчивость механизмов. На вибростенде проверяется сопротивляемость тряске. Кофр, нагруженный вдвое больше разрешённой массы, трясут с перегрузками до 50G непрерывно в течение 50 часов с частотами, характерными для мотоцикла, и имитирующими езду по грунтовкам, разбитому асфальту и брусчатке. Потом ещё 25 часов трясут с разрешённой нагрузкой внутри, и последние 25 часов трясут без груза. Если при расчётах прочности креплений и самого корпуса были ошибки, то они обязательно вылезают наружу трещинами и отрывом креплений. Такие кофры в производство точно не попадут.
После проверки прочности тестируется герметичность и стойкость к ультрафиолету. В этом испытании проверяется сопротивляемость мотоциклетного кофра тропическому ливню, хлещущему в специальной камере со всех сторон, чередующемуся с облучением кофра мощными ультрафиолетовым лампами. Продолжительность теста – 1500 часов. За это время не должен выгореть цвет пластика, но должна сохраниться сухость внутри.
Финальный этап тестирования – нахождение десять суток подряд в соляном тумане. Металлические элементы (оси петель и замки) не должны показать признаков коррозии.
После прохождения всех тестов на станке с ЧПУ делают молдинг, но уже не из дерева, а из металла. Для производства корпуса кофра таких форм нужно две (внутренняя и внешняя поверхность), ещё две для производства крышки. После изготовления их поверхность выравнивается от полосок прохода фрезы, полируется сначала вручную, потом электрохимическим способом для выведения в идеал. Матрица для литья стоит дорого, но служит долго, до 20 лет, и количество кофров, которые в ней можно изготовить, меряется десятками тысяч.
Пластик для производства кофров состоит из 95% гранул первичного пластика, 4% красящего пигмента и 1% вещества, защищающего от ультрафиолета. Последний компонент очень дорогой, но именно он гарантирует, что ваш чёрный кофр не станет через несколько лет серым. Литьё между двух половинок матрицы производится под давлением 1800 атмосфер (аналогичное давление будет на глубине 18 километров под водой). После того как всё пространство будет заполнено жидким пластиком, половинки дополнительно сжимаются прессом с усилием до 700 тонн на квадратный сантиметр. Это гарантирует отсутствие раковин, высокую прочность и однородную плотность материала в готовой детали.
Робот с присоской после вынимания из формы кладёт деталь на конвейер для её постепенного остывания. Иногда она остывает сама по себе, если форма не очень сложная, иногда внутрь приходится класть специальную деревянную вставку, чтобы при остывании не случилась деформация. В конце конвейера располагается цех сборки, где из уже холодных корпусов, крышек и фурнитуры собирают кофры и пакуют для отгрузки дилерам.
Путь от первых эскизов до первых серийных мотокофров обычно длится сакральные девять месяцев. Достаточный срок, чтобы сделать идеально крепкий, красивый и функциональный продукт, который будет радовать владельца долгие годы.